Refineries and terminals
Information to Insights, for safer, more profitable operation
Monitoring systems deliver accurate and timely corrosion rates.
Correlating changes in corrosion rates with changes in operating parameters creates insights enabling more informed decisions about
- feedstocks – including opportunity crudes
- production rates
- chemical inhibitor strategy
- turnaround timing
- metallurgical upgrades.
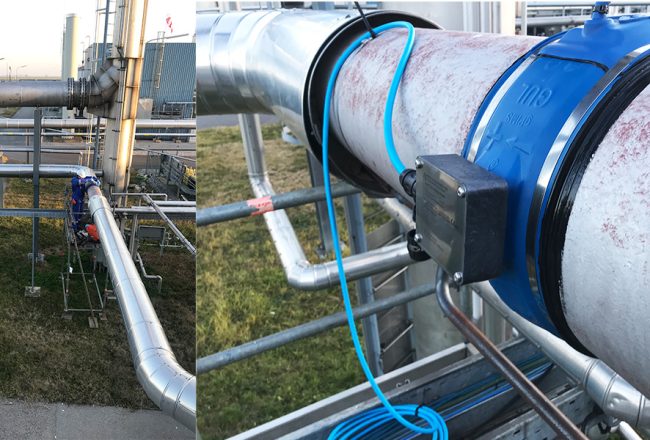
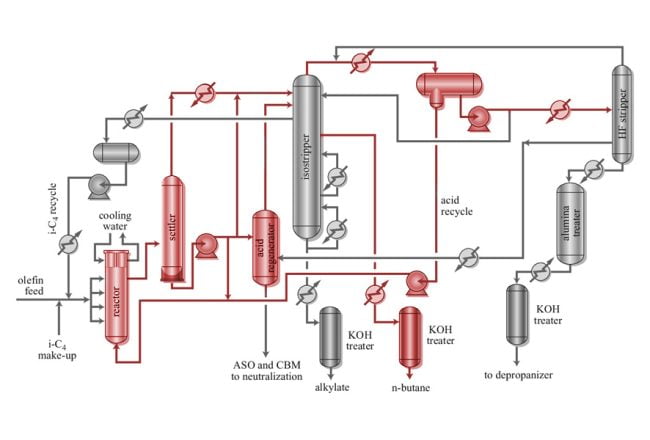
Safer operation
Managing HF Alkylation corrosion failure risk
Contact between highly concentrated acid and carbon steel forms a stable iron fluoride layer.
Contact with an acid/water mix forms an unstable and non-protective hydrate scale – this swells and can detach.
Process upsets – temperature or water content variations, or changes in feedstock quality changes – drive aggressive, transient corrosion.
More profitable operation
Avoiding unplanned outages in crude overhead lines
HCl, NH4Cl, amine hydrochloride salt corrosion
Visibility of corrosion rate, and correlating this with changes in process parameters informs mitigation
- desalter performance optimisation
- chemical inhibitor strategy
- dew point control
- feedstock blending
Example overhead configuration, with inhibitor injection and corrosion locations.
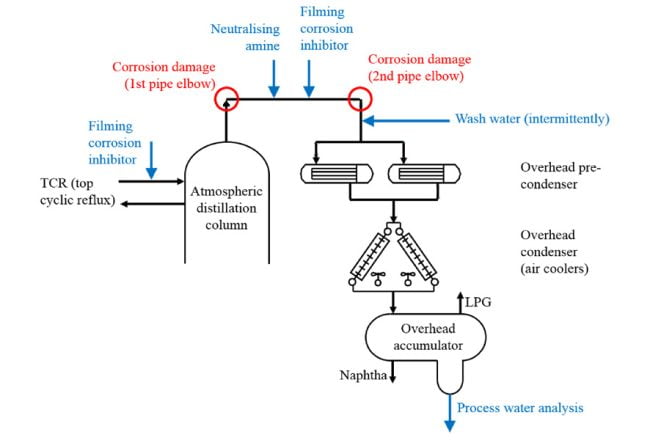
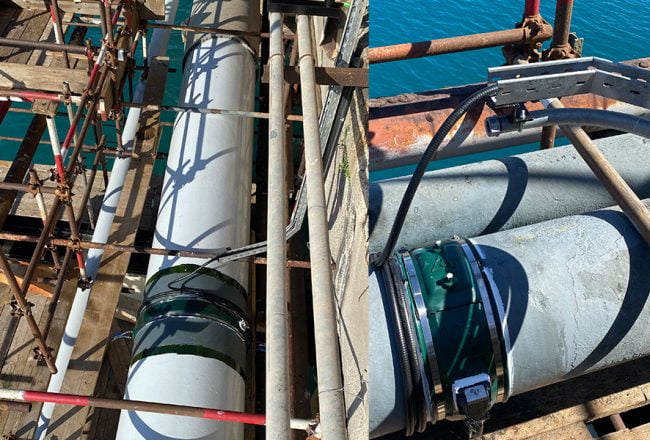
Guided Ultrasonics systems for downstream facilities
Flexibly meeting demanding requirements
- non-intrusive IP67 rated sensors, proven over years in maritime environments
- data retrieval with existing cabling, or wireless
- data analysis and visualisation at your desk – no hazardous data collection at height / hot pipework